Get Industry Focused Reports
Q.Shop provides you with a platform to collect your data consistently and coherently.
This mass of data is then translated into information for managers and decision-makers so they can take appropriate action.
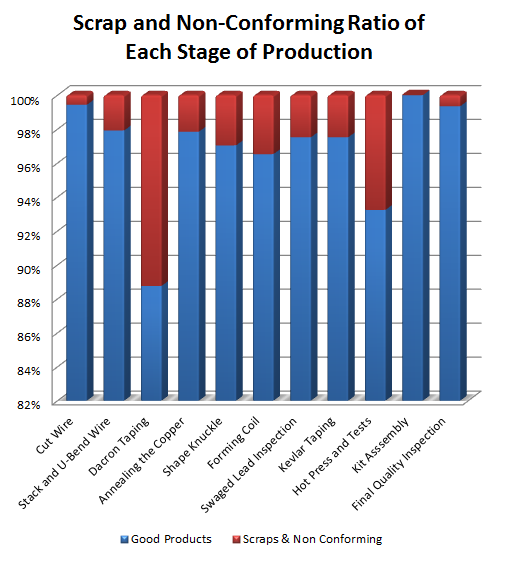
Unlimited Report:
- Various Chart Formats
- Custom Certificate Of Compliance
The availability of data at the fingertips of Engineering and Quality departments empowers them with an unprecedented level of ability to analyze and monitor any negative trend in your production. This information helps them take appropriate corrective action or implement an improvement plan before it turns into a major cost.
Internal Reports: A wide range of diverse and customized print formats can be defined for each customer or for each product as needed, and used over and over
Customer Reports: Generating compliance certificates or any other test report is a breeze as the system has no need for data entry or transferring data from one form to another. Anyone can simply key in the job number and all related data will be populated automatically in the compliance certificate.
Specialized reports toward:
- Repair Business
- Make-To-Order Manufacturing
As soon as a job is estimated and the scope of work is identified, unnecessary sections of the form are hidden from view, which makes it much easier for the operator to see and fill in what is needed.
This is the nature of repair business and make-to-order manufacturing, which are fully supported by Q.Shop’s optional and configurable forms.
Q.Shop forms will shrink or expand, according to the work scope, to collect only the relevant data.
This emphasizes one message, that employees should always fill in all the data in the form displayed.
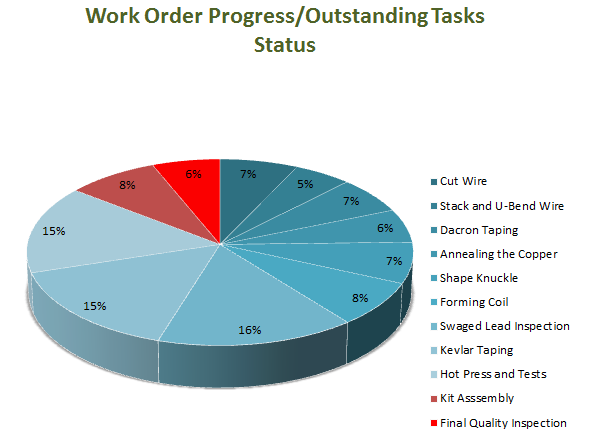
Simplifying Quality Inspection.
Measure, monitor, and manage quality data throughout the production cycle or repair and overhaul process. We offer production workforce management and document management solutions.
Q.Shop Report Dashboard:
Q.Shop gives the ability to analyze and monitor unusual trends in production.
This information helps save costs by taking appropriate corrective action and implementing an improvement plan before it turns into a major cost.
- Real-Time Bird’s-Eye View on Production
- Save Time and Uncover Hidden Costs
- Eliminate Work Stoppage and Idle Time
- Expedite and Facilitate Quoting
1- Real-Time Bird’s-Eye View on Production
Managers can track production progress in real-time. Customer service and sales personnel can respond to the customer’s inquiries without having to interrupt shop supervisors or technicians to get the latest job status.
2- Save Time and Uncover Hidden Costs
In one of our case studies, Q.Shop helped our client save 1 hour and 15 minutes on a 20-minute operation. Yes, Q.Shop seems to have broken the laws of physics, or maybe we just uncovered hidden costs that were eating up the bottom line and reducing profit.
3- Eliminate Work Stoppage and Idle Time
Shop supervisors and lead hands are instantly informed of any irregularity in the production and can take immediate action to rectify the situation and prevent work stoppage or delay.
4- Expedite and Facilitate Quoting
In repair shops, Q.Shop facilitates and expedites the estimating and quoting process. As soon as a job is inspected and estimated in the shop, the sales team is notified so they can prepare the customer quote and submit it for approval.